Stainless steel fine wire is essential across a wide range of industries, including electronics, medical devices, aerospace, filtration, and industrial mesh. In this article, we’ll walk you through the complete production process and the best equipment used to manufacture fine wire. You’ll also learn what to look for when choosing a manufacturer or supplier, and why many companies are turning to reliable partners in China to strike the right balance between cost, performance, and quality.
What Size Is Stainless Steel Fine Wire?
Stainless steel fine wire typically refers to wire with diameters ranging from 0.01 mm to 0.5 mm, depending on the application. Generally, ultra-fine wire is classified as below 0.05 mm, fine wire ranges from 0.05 mm to 0.2 mm, and small-diameter wire falls between 0.2 mm and 0.5 mm. Different industries follow specific standards: medical applications often require wire between 0.02 mm and 0.2 mm, electronics from 0.01 mm to 0.3 mm, filtration from 0.03 mm to 0.5 mm, and aerospace from 0.05 mm to 0.25 mm. Medical-grade wires—such as those used on operating tables—are typically thinner and demand higher precision and surface quality, which means you’ll need a high-precision wire drawing machine to ensure reliable and consistent results.
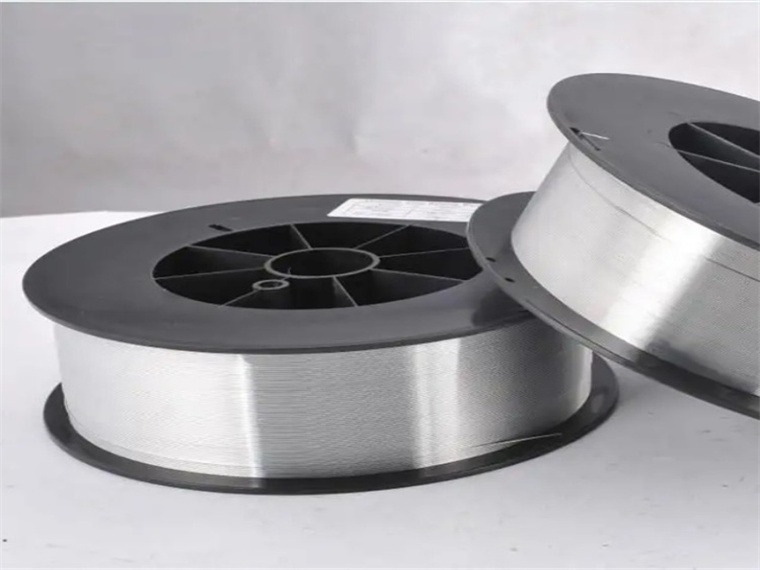
Understanding Stainless Steel Fine Wire Drawing Production
Producing stainless steel fine wire requires either a single stage or multiple stages of precision drawing machines. At each stage, the machine uses specialized dies to gradually transform raw stainless steel rods into fine wire with diameters ranging from several millimeters down to just a few microns. Industries such as medical, electronics, aerospace, and filtration demand different wire sizes and performance standards. For example, medical-grade wires—especially those used on operating tables—are extremely thin and require exceptional surface quality. To meet these demands, manufacturers rely on high-precision wire drawing machines. Sky Bluer, a trusted manufacturer in China, specializes in advanced wire drawing equipment designed to deliver the accuracy and reliability needed for producing stainless steel fine wire across various critical applications.
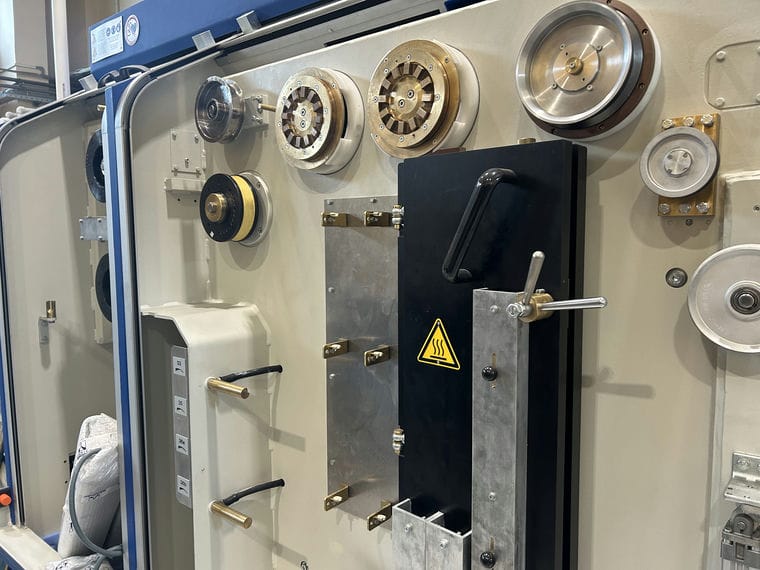
Here’s a breakdown of the core equipment involved:
- Wire Drawing Machine
- The wire drawing machine is the core component of any fine wire production line. It gradually reduces the diameter of stainless steel rods by pulling them through a series of tungsten carbide or diamond dies, or through a precision rolling cassette. This modern structure has gained widespread recognition among customers, many of whom are moving away from using older annealing equipment in their existing facilities. As a result, the process now often goes directly from drawing to coiling, eliminating the need to transfer materials to a separate workshop for annealing. This streamlined workflow significantly reduces labor requirements and saves valuable production time.
- Purpose: Reduces wire diameter/Thickness while increasing length.
- Key Features: High-speed operation, automatic lubrication, die cooling system.
- Best For: Achieving uniform wire thickness with minimal surface defects.
Brand CRM new wire drawing machines often include inline annealing systems to soften the wire during drawing, which is essential for ultra-fine wire applications.
- Annealing Furnace
After drawing, the stainless steel wire needs heat treatment to relieve internal stress and restore ductility. This is done using an annealing furnace.
- Types: Inline annealing, induction annealing, and continuous tube annealing.
- Best Option: Continuous tube annealing furnaces offer high throughput and consistent results.
- Key Feature: Inert gas environments (e.g., nitrogen or argon) to prevent oxidation.
Investing in a high-quality annealing system ensures long-term benefits by delivering optimal wire flexibility—crucial for medical-grade and electronic applications. In addition to manufacturing wire drawing machines, we produce a wide range of annealing equipment, from compact units to large-scale systems. We customize the annealing equipment to meet your specific production needs and wire surface quality requirements, providing the best solution for your operation.
- Cleaning and Pickling Line
Cleaning and pickling lines for stainless steel wire come in different types based on production needs. Batch lines treat wire in chemical baths and suit smaller or specialty batches but work slower. Continuous lines move wire through tanks for cleaning and drying, ideal for large-scale production with consistent results. Spray lines use high-pressure sprays for gentle and precise cleaning, good for delicate wires. Electrochemical pickling lines add electrical current during cleaning for a smoother surface, often used for high-quality wires. Manufacturers select the type based on production volume, wire type, surface quality, and environmental factors. Function: Removes lubricants, oxides, and other impurities.
- Fine Wire Rolling Mill (Optional for Shaped Wire)
In some cases, customers require shaped wire—such as flat, square, or wedge profiles. This is where a fine wire rolling mill becomes essential.
- Capabilities: Produces precision flat or custom-shaped wire profiles.
- Ideal Manufacturer: Look for a supplier that offers adjustable rolling gaps and high-precision forming capability.
- Best For: Applications like heating elements, watch springs, and surgical tools.
A quality manufacturer integrates real-time thickness monitoring to maintain tight dimensional tolerances.
- Spooling and Take-up System
Once the stainless steel wire reaches its final diameter and properties, it needs to be carefully wound onto spools or coils.
- Types: Single/double-spool take-up systems, basket winders, tension-controlled payoffs.
- Best Systems: Use programmable logic controls (PLCs) and servo motors to manage tension and prevent tangling.
Wire damage during spooling can ruin the entire batch. That’s why choosing the best equipment here is just as important as in earlier stages.
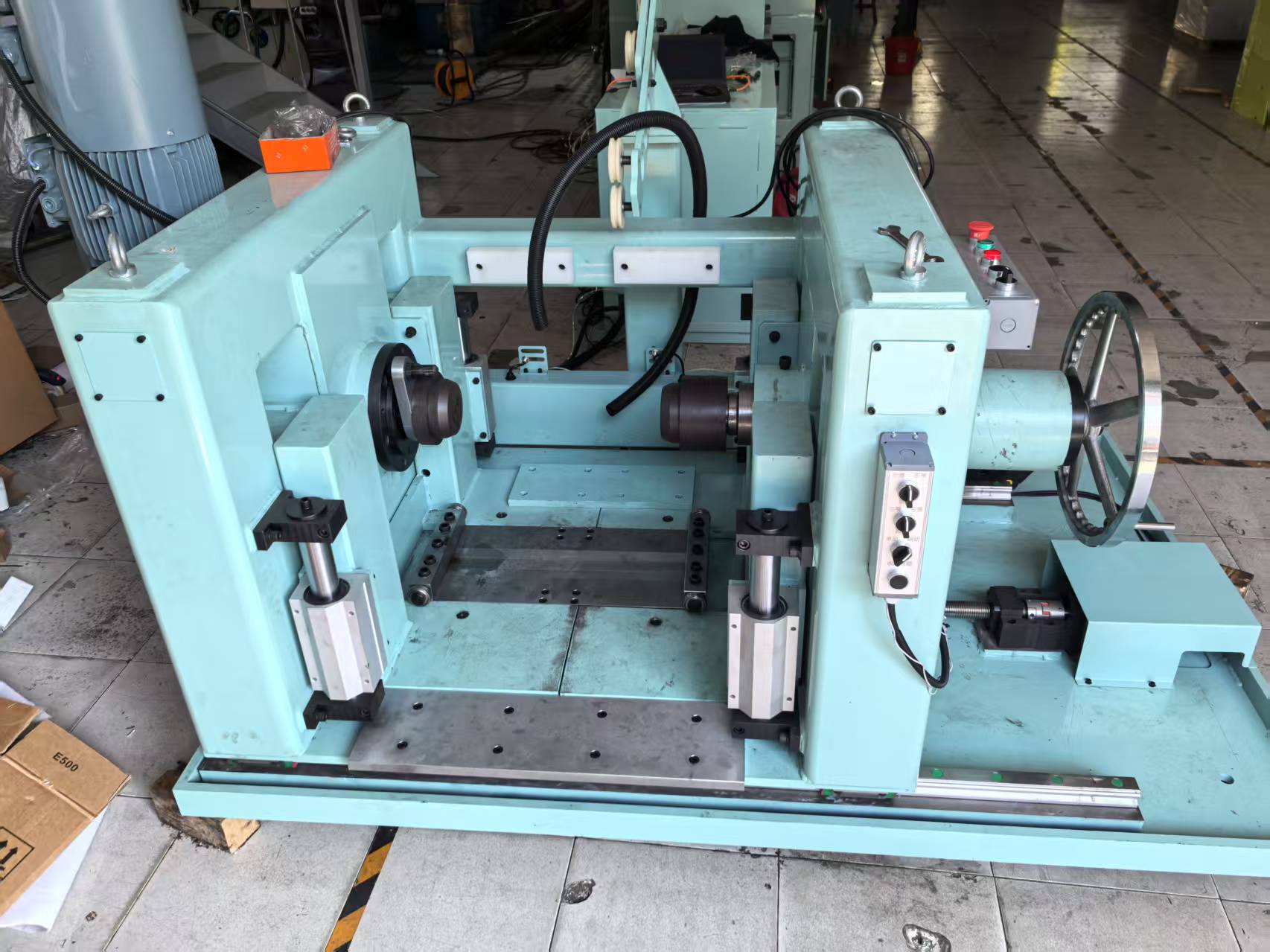
Electrical Configuration of Our Stainless Steel Fine Wire Drawing Machines
We have detailed the main machine models used to produce stainless steel fine wire. Some users may be particularly interested in the electrical configuration of the wire drawing machines we manufacture. Here is an overview:
- We use Schneider or Inovance inverters for reliable motor control.
- The machines feature Siemens S7-300 PLC with PROFIBUS communication, and the operation panel includes a 10-inch color touchscreen for metering, control parameters, and fault display.
- Each control panel supports linkage, start/stop control, and the footswitch offers front and rear connection, as well as forward and reverse inching functions. Every group is equipped with a wire break protection device for safety.
- The machines can be produced on demand to meet your schedule.
- The electric control cabinet includes LED tube lighting that automatically turns off when the cabinet door is closed.
- Key electrical components—such as the main power switch, contactors, relays, buttons, and signal lights—are from Schneider or Chint. Sensors are sourced from French TE, the footswitch is explosion-proof and dustproof, and motors come from the trusted Wuxi Hengda brand.
- The cabinet design follows international standards with a logical layout, standardized wiring, and neat installation for easy maintenance and safety.
This robust and carefully engineered electrical setup ensures reliable, efficient, and safe operation of our wire drawing machines.
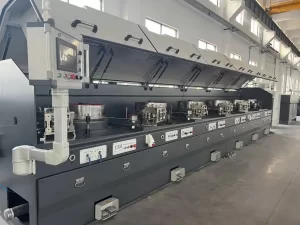
Company Profile:
Sky Bluer Environmental Technology Co., Ltd. stands at the forefront of precision metal wire processing as a premier manufacturer of advanced cold rolling and wire drawing machinery. Our comprehensive portfolio features state-of-the-art fine wire drawing machines, intermediate and rod breakdown drawing systems, as well as cutting-edge wet and dry drawing technologies. We also specialize in sophisticated wire flattening and shaping lines, alongside industry-leading photovoltaic (PV) ribbon and busbar production equipment. With a steadfast commitment to innovation, quality, and customization, Sky Bluer delivers turnkey solutions that empower clients worldwide to achieve unparalleled precision, efficiency, and performance in their metal wire manufacturing operations.