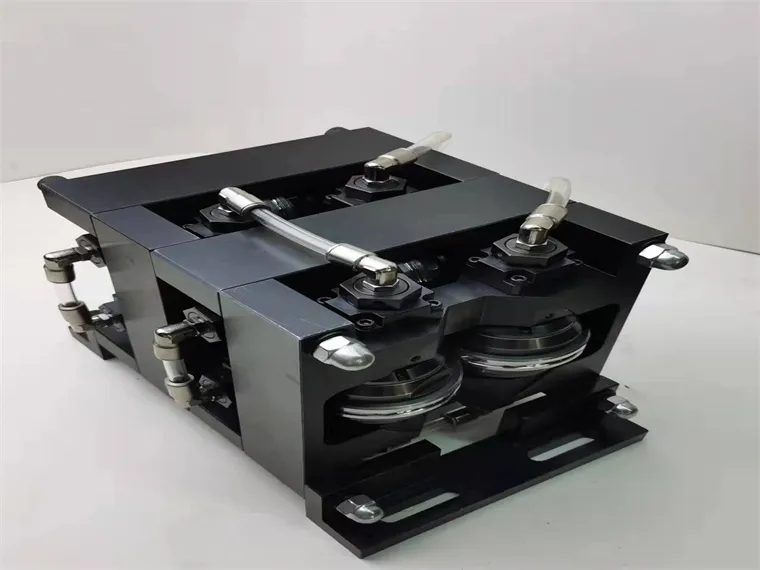
Flux Core Welding Wire Production Line
The Flux Core Welding Wire Production Line, as known as welding wire drawing machine, designed by the CRM Team, is engineered to efficiently handle the production of flux-cored welding wire. This advanced line enables key processes such as drawing, cold rolling, and cold drawing of flux-cored welding wire.
Main Features
- Strip uncoiling;
- 4-block strip and wire cold flattening and shaping station with motorized rolls;
- Multipass drawing with cold rolls cassettes;
- Welding wire Straightening
- Welding wire polishing
- Wire spooling.

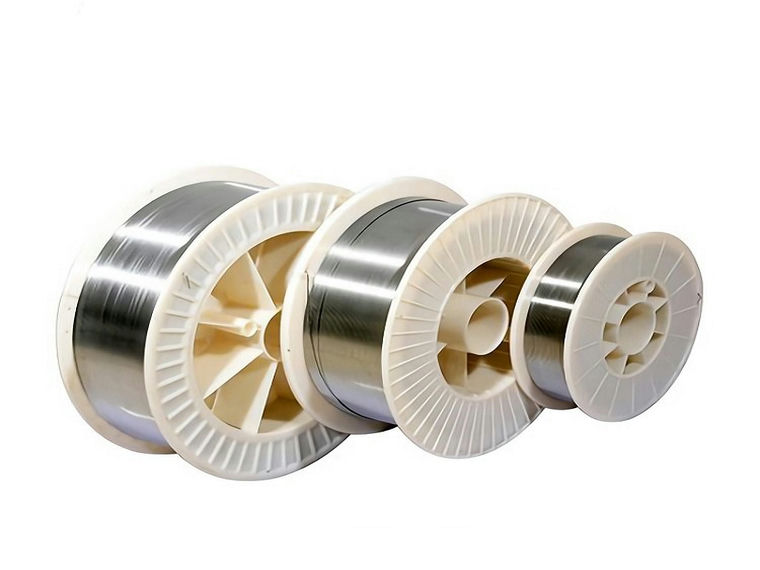
What Sizes of Flux-Cored Wire Can the Machine Produce?
The CRM2025-WW drawing machine is capable of producing flux-cored wires in a wide range of sizes to meet various welding needs. Common sizes typically include diameters such as 0.8 mm, 1.2 mm, 1.6 mm, 1.8mm 2.0mm,2.4mm,2.8mm,3.2mm,and 4.0mm. but the machine can be customized to produce other sizes based on specific requirements.
This flexibility ensures the machine can support diverse applications, from fine wire welding to heavy-duty industrial projects.
What Is The Production Process For Flux Core Welding Wire Production Line
- Steel Strip Preparation: Process from raw steel strips to flux-cored wire, If you are interested in the quality of the finished product, we recommend that you also choose high-quality raw materials
- Cold Rolling & Drawing: The traditional way is to use a wire drawing die to produce flux-cored welding wire, but in order to achieve high quality requirements, we all use D-type cassette roller dies CRM2025-D produced by our company.
- Flux Core Filling: Flux is added to the wire through a precise process during the production stages. To ensure smooth operation and consistent quality, we incorporate tension adjustment and straightening equipment after each pay-off machine. This setup guarantees proper speed synchronization, preventing any disruptions and ensuring the flux is evenly applied to the wire for optimal performance.
- Inline annealing: Annealing and drawing processes significantly improve the performance of stainless steel flux-cored wire. These annealing processes enhance the wire’s plasticity and toughness, making it easier to handle during welding. They also create a uniform and dense structure, improving the wire’s mechanical properties and corrosion resistance. By optimizing the drawing parameters, we can control the wire’s diameter and surface quality, ensuring it meets all of your various welding requirements.
- Coiling & Packaging: Final collection in coils with appropriate weight and packaging We can provide standard take-up equipment or customize it to meet your specific requirements.The production process starts with steel strips and proceeds through multiple stages, ultimately resulting in flux-cored welding wire neatly collected in coils of the desired weight. This streamlined and precision-focused design ensures high-quality output, meeting the demands of modern welding applications.
Industries Using Flux-Cored Welding Wire Production Lines
Flux-cored welding wire production lines actively support industries that demand high-quality welding. Manufacturers in the automotive sector assemble and repair vehicles using these wires. Construction and infrastructure companies rely on them to build bridges, pipelines, and steel structures with strength and reliability. Shipbuilders use these wires extensively to construct and maintain ships and offshore platforms. Oil and gas operators weld pipelines, pressure vessels, and storage tanks with flux-cored wires, ensuring durability in harsh conditions. In manufacturing and heavy equipment production, these wires deliver the precision and strength needed for machinery, industrial components, and agricultural equipment. Energy companies also employ them in power plants, renewable energy installations, and energy storage systems. Beyond these, many other industries can benefit from using flux-cored welding wires for their critical applications.
After-Sales Service for Flux Core Welding Wire Production Line
We offer fully customized wire take-up machines tailored to your specific requirements, including your finished product’s packaging method, weight, and size. Whether you need solutions for compact spools, large reels, or unique packaging formats, our designs ensure optimal efficiency, durability, and seamless integration into your production line.
What services do we offer after you purchase our equipment?
1. Installation & Setup:
Our team provides full installation and commissioning services, ensuring the production line is set up properly and runs at peak performance from the start.
2. Staff Training:
We offer in-depth training for your team, covering operation, maintenance, and troubleshooting to ensure efficient use of the equipment.
3. 24/7 Technical Support:
Our technical support team is available to assist with any issues, providing remote assistance or on-site visits as needed to ensure minimal downtime.
4. Spare Parts Availability:
We maintain a comprehensive stock of spare parts and can quickly supply any components required for repairs or maintenance, reducing production interruptions.
5. Scheduled Maintenance:
Regular maintenance services help keep your production line in optimal condition, preventing unexpected breakdowns and maximizing efficiency.
6. Upgrades & Optimization:
We offer upgrades and process optimizations to keep your Flux-Cored Welding Wire Drawing production line aligned with the latest technology and meet evolving industry standards.
7. Warranty & Repair:
Our equipment comes with a warranty, and if any issues arise, our team is ready to provide fast repair services to restore full functionality.
With our dedicated after-sales support, we ensure your Flux Core Welding Wire Production Line continues to perform reliably and efficiently throughout its lifetime
Related Products
Frequently Asked Questioins
Our company is based in China and specializes in providing turnkey projects.
Solid welding wire is made entirely of a single metal, such as steel, stainless steel, or aluminum. It features a straightforward structure as a uniform solid cylinder. For instance, ER70S-6 solid welding wire, primarily composed of low-carbon steel, is specifically designed for welding standard structural steel.
In contrast, flux-cored welding wire comprises a metal sheath and an internal flux core. The outer sheath, typically made from low-carbon steel strip, encases the flux core, which contains various components such as arc stabilizers, slag formers, deoxidizers, and alloying agents. An example is E501T-1 flux-cored welding wire, which features a thin steel strip outer sheath and a flux core enriched with minerals and alloying elements. This composition ensures excellent welding performance for structural steel applications.
Yes, This equipment is designed to meet the modern market's growing demand for cladding and fine wire products. It represents a cutting-edge production line tailored for manufacturing both solid welding wire and flux-cored welding wire. The machine efficiently processes steel strips with a thickness of 0.3mm or 0.4mm and a width of 13mm or 14mm.
By intelligently optimizing the number of rollers in the rolling mill frame, selecting the appropriate number of wire drawing tanks, and precisely integrating the rolling and drawing processes, the equipment can produce Φ1.6 mm finished cladding flux-cored welding wire in a single, seamless operation. This innovative design ensures high efficiency and precision, catering to the evolving needs of the welding industry.
The key feature is that we design and offer two types of flux-cored wire production lines to cater to diverse your needs
1. Traditional Split Structure:
This design separates the wire rolling, rough drawing, and finishing drawing processes.
2. Integrated Rolling and Drawing System:
This modern system designed by our CRM team which can directly connects rolling and drawing processes, enabling seamless production.
So You can select the production line that best suits your product requirements, factory layout, and specific needs.
We use large rolls of heavy steel strips to enhance rolling mill efficiency and minimize auxiliary downtime. In the integrated rolling and drawing system, we increase the finished product take-up speed to 60m/s or higher, ensuring precise coordination between wire forming and drawing.
We equip the system with a forced lubrication feature to boost wire drawing speeds while maintaining stability during high-speed operations. This setup enhances surface quality, reduces fine wire breakage, and ensures smoother production. With this integrated machine, you can achieve a daily output of over 36 tons and an annual production capacity of 5,600 tons, delivering high-efficiency, large-scale manufacturing solutions.
We Are Trusted Over 16+ Countries Worldwide
Our company is based in China and specializes in providing turnkey projects. We focus on the research, development, and manufacturing of complete flux-cored wire production lines and solid welding wire production equipment. Our main welding material products include seamless flux-cored wire, flux-cored wire, solid welding wire, welding rods, flux, and complete manufacturing equipment for flux-cored and solid welding wires,fine wires,flat wire and shaped wires with high accuracy.
We offer a comprehensive range of welding materials, covering carbon steel, low-alloy steel, stainless steel, aluminum-based, copper-based, nickel-based, and surface cladding products. Throughout the production process, we strictly adhere to international quality management system standards, ensuring exceptional product quality and reliability.