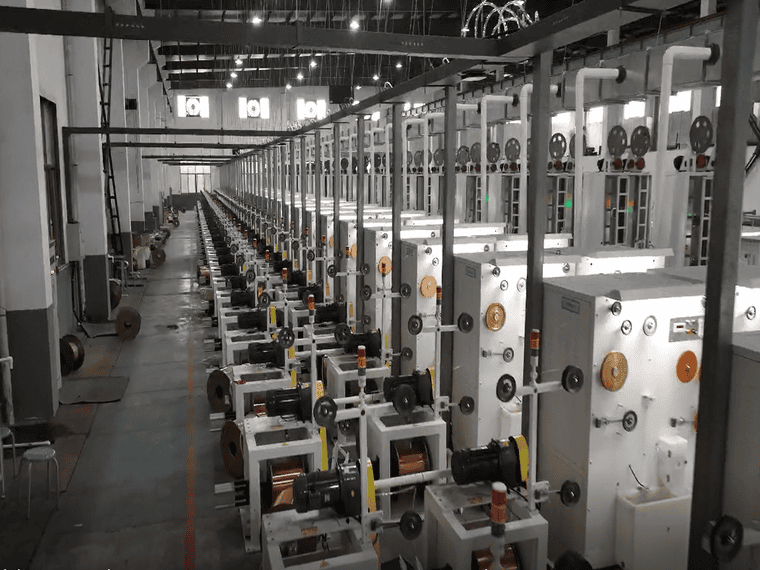
Copper PV Ribbon Machines
Welcome to Sky Bluer Solar Equipment! Our factory specializes in providing turnkey solutions for PV ribbon manufacturers. Whether you’re looking for a high-quality PV ribbon machine or seeking innovative solutions for your solar ribbon manufacturing process, Sky Bluer Industries offers a wealth of expertise and resources for professionals in the PV ribbon industry.
Details of Copper PV Ribbon Machines
- The typical size range of copper PV ribbon machines.
- Manufacturing Process of Copper PV Ribbons
The typical size range for Copper PV Ribbon machines.
Thickness:0.07mm-0.2mm
Width:1mm-3mm
Base Metal:Fri | Buy | CCA
Solder Type:Sec; SnPb; SnAg; SnCuAg; SnPbAg; SnBi; SnBiAg
Busbar/Bussing wire is the wire that connects the accumulated current to the junction box or electrical distribution system.
Thickness:0.07mm-0.5mm
Width:3mm-6mm
Base Metal:Fri | Buy | CCA
Solder Type:Sec; SnPb; SnAg; SnCuAg; SnPbAg; SnBi; SnBiAg
Thickness: 0.080 – 0.500 mm
Width: 1.000 – 5.000 mm
Coating Thickness: 10 – 40 µm
Copper Core Material: Cu-OF
Coating Material: Bare, Sn 100, Sn63Pb37, Sn62Pb36Ag2
Material types: Lead Free Ribbon, Copper Ribbon, Tin Coated Copper Ribbon
The manufacturing process of copper PV ribbons begins with raw material preparation, where high-purity copper—typically 99.99% oxygen-free—is fed into the production line via a payoff machine. The purity of the copper is a critical factor in determining the quality of the final welding strip.
Next, the ribbons undergo annealing, a heat treatment process that enhances their ductility and flexibility. To improve solderability and prevent oxidation, a tin coating machine applies a uniform layer of tin. The ribbons are then straightened and precisely cut to the required lengths.
Following this, rigorous quality inspections are conducted to ensure optimal conductivity, accurate thickness, and strong coating adhesion. Finally, the finished ribbons are spooled, packaged, and labeled, ensuring they are ready for safe transportation and reliable use in photovoltaic applications.
Copper PV Ribbon Machines: Precision Equipment for Solar Panel Manufacturing
Copper PV ribbon machines are specialized equipment designed for the production of high-performance copper-based PV ribbons used in solar panels. These systems include a payoff machine for feeding raw materials, rolling mills for precise thickness reduction of flat ribbon wires, and annealing furnaces to enhance ductility. Additionally, tin coating systems improve solderability and corrosion resistance, while a take-up machine efficiently packs the finished product. These advanced turnkey manufacturing solutions are essential for producing reliable, high-conductivity interconnect ribbons and busbars, ensuring superior performance in photovoltaic applications.
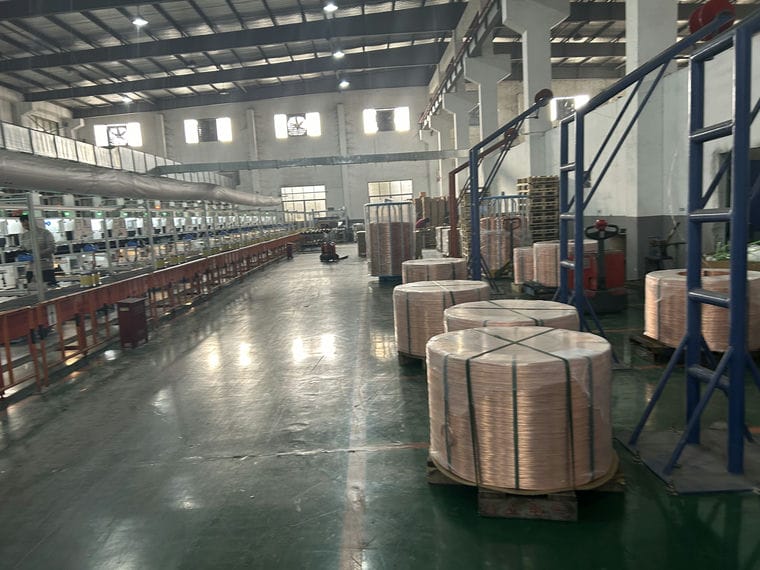
Advantages of Copper PV Ribbon Machines
1. Efficient Processing: The machine transforms round copper wire into high-quality photovoltaic ribbon through a precise process that includes annealing, cleaning, hot-tin coating, cooling, and precision winding.
2. Superior Coating Quality: Ensures uniform tin coating thickness, a glossy surface, and eliminates defects such as tin beads (slag) and pinholes, guaranteeing stable and reliable quality.
3. User-Friendly Operation: Features an intuitive human-machine interface (HMI) with a built-in round wire mode, making the system easy to operate and control.
4. High Mechanical Performance: Designed for durability, the ribbon maintains a yield strength of ≥56MPa, ensuring excellent mechanical stability and performance in photovoltaic applications.
Turnkey Solutions for Copper PV Ribbon Machines
Sky Bluer provides comprehensive turnkey solutions for copper PV ribbon machines, delivering a fully integrated production system from raw material processing to final packaging. Beyond equipment, we offer end-to-end support, including factory site selection and facility design, ensuring optimal layouts for water, flooring, walls, electricity, and gas systems. With a strong industry presence, we have successfully implemented complete solutions for 28 copper PV ribbon manufacturers worldwide. Moreover, our turnkey services cover installation, training, and continuous technical support, guaranteeing smooth and efficient operations. By choosing Sky Bluer’s turnkey solutions, manufacturers can accelerate setup, optimize workflows, and maintain consistent product quality, making it the ideal choice for high-performance copper PV ribbon production in the solar industry
Frequently Asked Questioins
Our company, headquartered in China, specializes in delivering turnkey solutions for PV ribbon and Busbar production lines. We are dedicated to the research, development, and manufacturing of complete, high-performance machinery, ensuring efficiency and precision in every project.
Common types of photovoltaic (PV) welding ribbons used in solar panel manufacturing include: Flat Ribbon/MBB Ribbon/SMBB Ribbon
PV Busbar
Black Busbar
Tin-Plated Copper Ribbons
Aluminum Ribbons
Bimetallic Ribbons
The speed of PV ribbon machines typically varies between 100 to 500 meters per minute, depending on the machine type and process complexity. Machines optimized for higher efficiency and automation usually operate at the faster end of the spectrum, while those involving more intricate processes, such as coating or precision shaping, may run at slower speeds. Additionally, factors such as the required quality of the ribbons, the materials used, and specific product types (such as fine-sized ribbons, flat wire, busbars, or black ribbons) all influence the speed. The level of automation in the system also plays a significant role in determining production speed.
In photovoltaic ribbon equipment, manufacturers use various types of flux to ensure effective soldering. Rosin flux is commonly chosen for its excellent solderability and minimal residue. On the other hand, water-soluble flux is preferred for its environmental benefits, as it can be easily cleaned after soldering, making it ideal for automated systems. No-clean flux leaves minimal residue and reduces the need for post-production cleaning. For tinning copper ribbons, organic acid flux is frequently used, providing strong solder joints and preventing oxidation. Additionally, activated flux contains chemical activators that remove oxide layers, ensuring a superior bond. The selection of flux depends on the ribbon type, soldering process, and the required level of cleanliness.
- 0.20 ± 0.010 mm
- 0.26 ± 0.010 mm
- 0.27 ± 0.010 mm
- 0.29 ± 0.010 mm
- 0.32 ± 0.010 mm
Our PV ribbon line produces a wide range of interconnect ribbons and busbars, typically 0.6 mm to 8 mm wide and 0.1 mm to 0.5 mm thick. We apply a 20-micron thick solder coating to the ribbons, with a tolerance of ±3 microns. The line also allows us to manufacture ribbons with various yield strengths—Rp0.2% below 60 MPa, 70 MPa, or 80 MPa, and in some special cases, even below 50 MPa—to meet different customer requirements.
Playlist
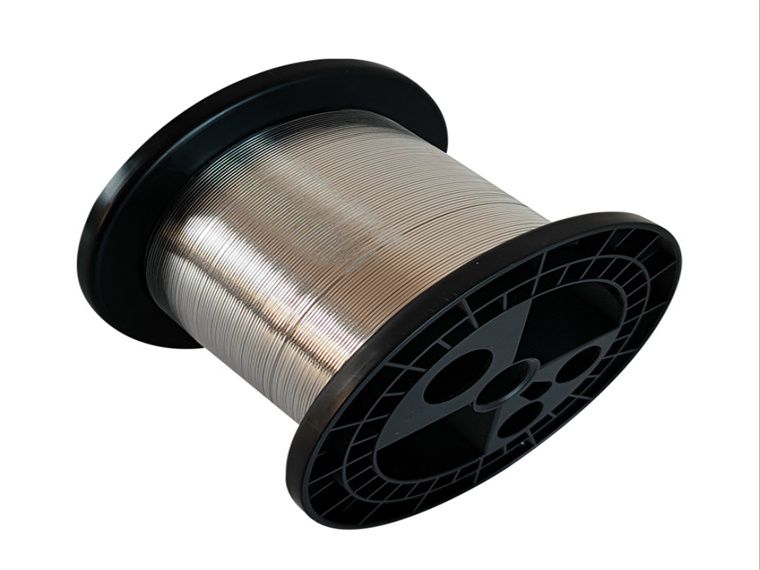
0:16
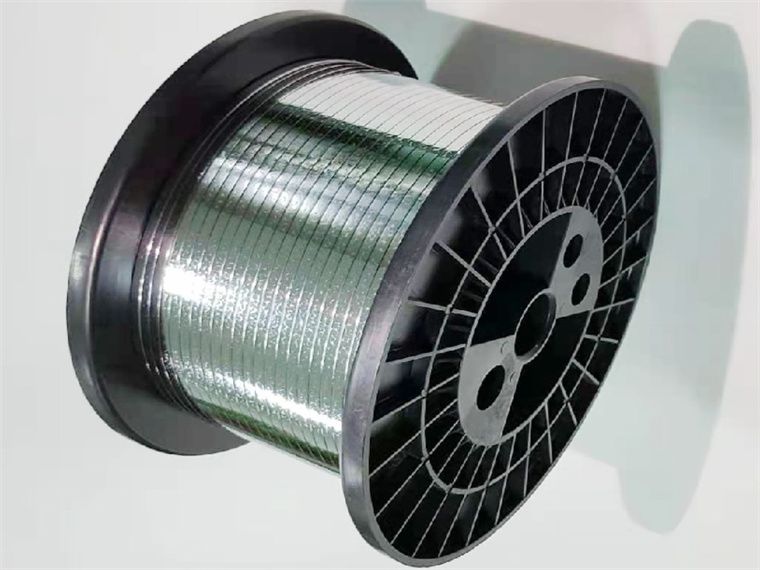
0:16
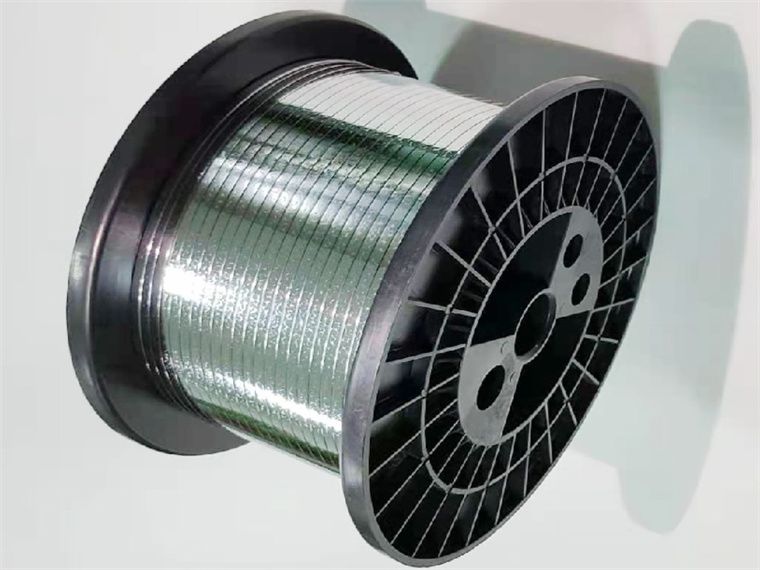
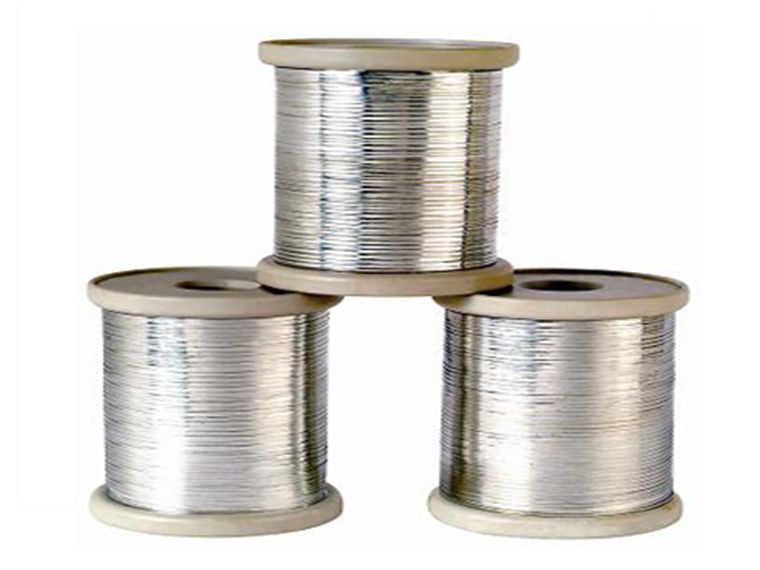
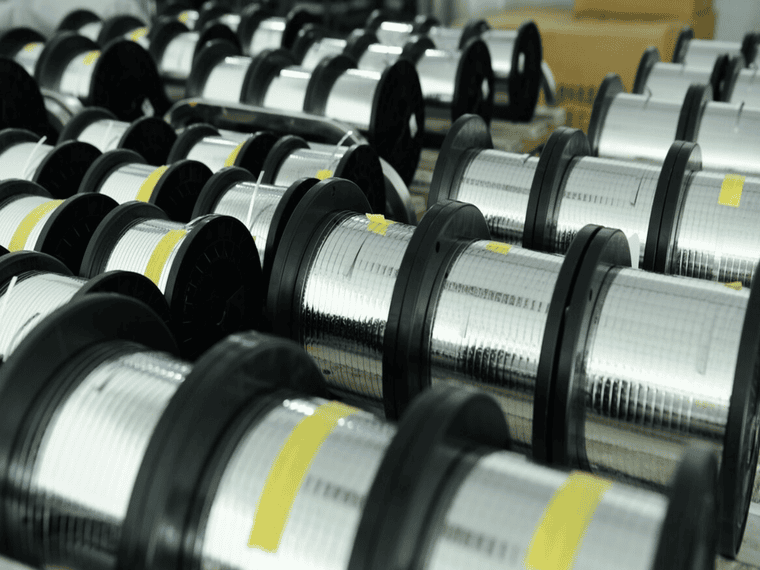