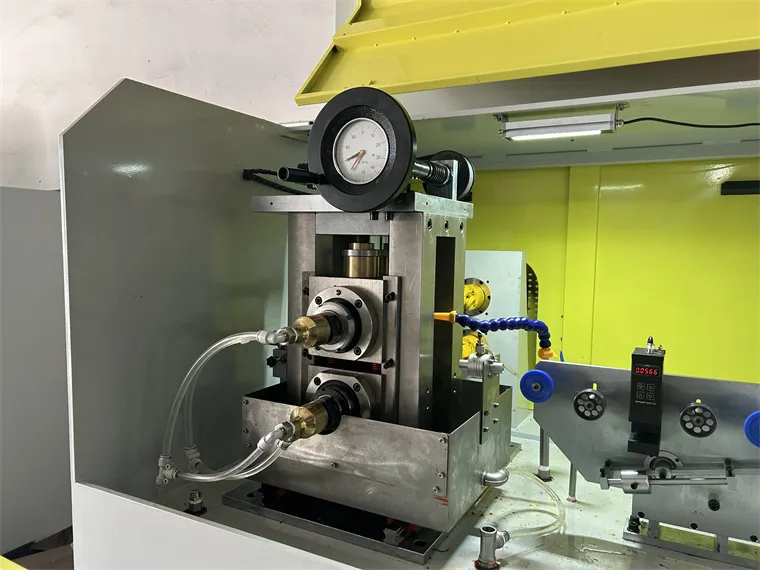
Aluminum Strip Cold Rolling Machine
Sky Bluer China specializes in the manufacturing of aluminum strip cold rolling machines designed to deliver precise thickness reduction and superior surface finishing. Our product range primarily includes both single-layer and composite aluminum strip rolling mills.
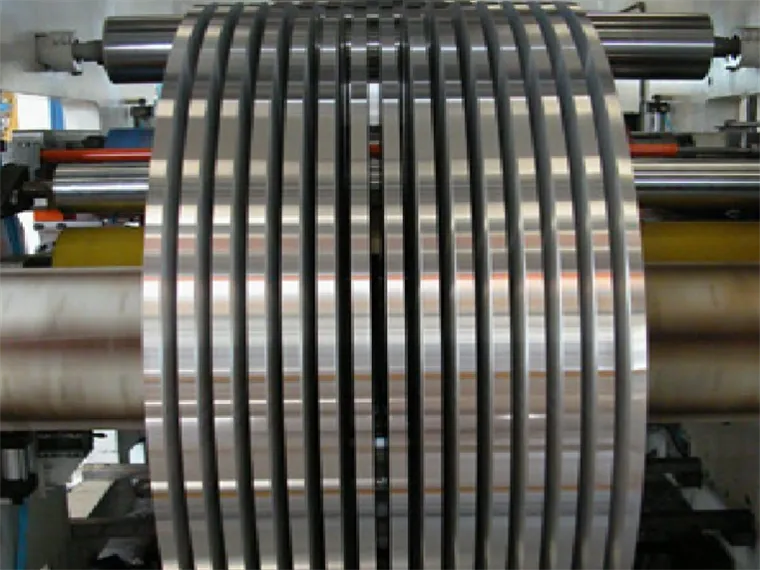
Composite Aluminum Strip Rolling Mill
Sky Bluer China manufactures composite aluminum strip rolling mills that are engineered to process multi-layer bonded metals—such as aluminum combined with copper, stainless steel, or other aluminum alloys. These rolling machines roll laminated materials into thin, uniform strips while ensuring strong interlayer bonding, precise thickness control, and high surface quality.
Ideal for applications in battery tabs, heat exchangers, clad metals, and electrical components, our composite rolling mills deliver consistent performance through advanced tension management, precision rollers, and customizable configurations tailored to your production needs.
Aluminum Strip Rolling Mills Manufacturer from China
A composite aluminum strip rolling mill consists of several key components designed to work together efficiently to reduce the thickness of aluminum strips and improve surface quality.
Examples by Application:
- Packaging Foil: 0.01–0.03 mm
- Electronics/Heat Sinks: 0.1–0.5 mm
- Automotive Panels: 0.5–2.0 mm
- Transformer Strips: 0.2–0.35 mm
- Typical Output Sizes of Aluminum Strip Cold Rolling Mills
- Key Components of a Composite Aluminum Strip Rolling Mill
- Typical Output Sizes:
Thickness:
From 2.0 mm down to as thin as 0.05 mm
(Some ultra-thin lines can reach 0.01 mm, depending on precision) - Width:
Typically ranges from 50 mm to 800 mm
(Custom machines can handle up to 1250 mm or more) - Length:
Continuous strip, coiled — the length depends on coil size and customer requirement - Customized size
Here are the main components:
1. Rolling Stands
• Function: These are the core components where the aluminum strip undergoes compression and thickness reduction. The stands are typically arranged in tandem and can include both single-layer and multi-layer rolling systems.
• Types: 4-high mills (four rolls), 6-high mills, and Cluster mills are common.
2. Drive System
• Function: Provides the power to rotate the rolls and move the aluminum strip through the mill. It usually consists of electric motors, gearboxes, and couplings.
• Control: It often integrates with the mill's PLC system to adjust speed and torque.
3. Rolls
• Function: The rolls are responsible for deforming the aluminum as it passes through them. For composite rolling mills, multiple rolls of different sizes are used for roughing and finishing passes.
• Types: Work rolls, Backup rolls, and Intermediate rolls are used depending on the design.
4. Hydraulic System
• Function: Controls the force applied between the rolls and adjusts the gap according to the thickness of the aluminum strip.
• Components: Includes hydraulic cylinders and valves for precise control.
5. Automatic Gauge Control (AGC) System
• Function: Monitors and adjusts the gap between rolls in real-time to ensure consistent strip thickness.
• Components: Includes thickness gauges, sensors, and a feedback loop to automatically regulate the roll gap.
6. Cooling and Lubrication System
• Function: Provides essential cooling and lubrication to reduce friction between the rolls and the aluminum strip, ensuring smooth operation and extending the lifespan of the equipment.
• Components: Includes cooling towers, oil pumps, and spray nozzles.
7. Tension Control System
• Function: Maintains proper tension throughout the rolling process, preventing the strip from breaking or wrinkling.
• Components: Includes tension sensors, winches, and motorized tensioners.
8. Coiler and Uncoiler
• Function: These are used to unwind the aluminum coil before rolling and then wind it back into coils after the rolling process is completed.
• Components: Includes coil reels, uncoiling stands, and winding machines.
9. Exit or Delivery System
• Function: Delivers the finished aluminum strip to the downstream processing stage.
• Components: Includes exit rolls, guiding rollers, and cooling beds.
10. Automation and Control System
• Function: Coordinates and optimizes the operation of the entire rolling mill. It ensures smooth adjustments to speed, pressure, and tension, and integrates all components into a cohesive system.
• Components: Includes PLC systems, HMI (Human-Machine Interface), and sensors.
Basic Function of Aluminum Strip Cold Rolling Machine
The primary function of an Aluminum Strip Cold Rolling Machine is to reduce the thickness and enhance the surface finish of aluminum strips by passing them through precision rollers at room temperature. The basic process involves rolling aluminum round bars or flat bars into flat, uniformly sized strips.
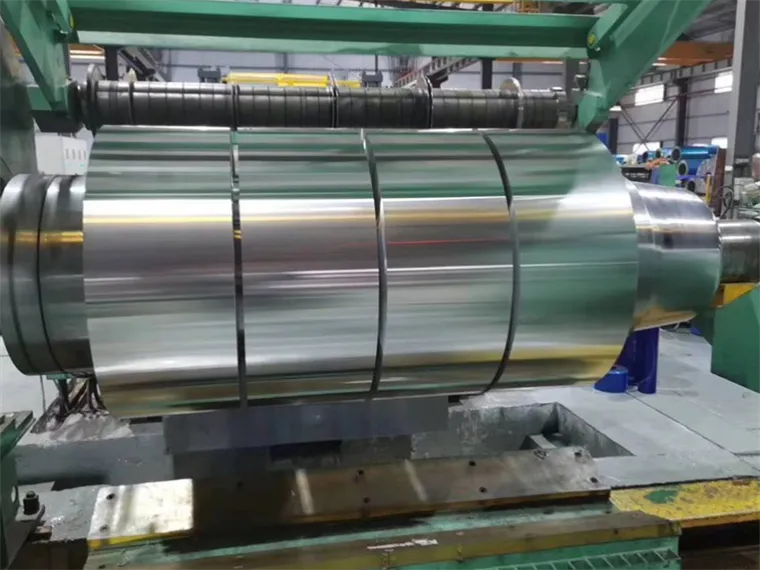
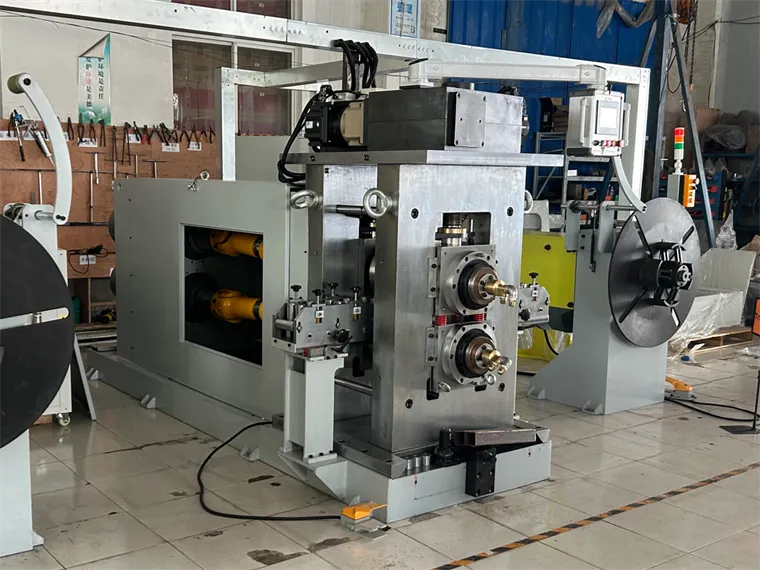
Cold Rolling Strip Mills by Sky Bluer China
Sky Bluer China manufactures cold rolling strip machines designed to reduce the thickness and enhance the surface finish of metal strips, such as aluminum, steel, or copper, by passing them through a series of precision rollers. We offer various types of rolling mills, including two-high rolling mills, four-high rolling mills, and multi-stage rolling mills, each tailored to provide precise control over material thickness and surface quality, ensuring high performance for a wide range of industrial applications.
Applications About Aluminum Strip Cold Rolling Machine
The aluminum strip cold rolling machine serves a broad range of industries with its ability to produce high-precision, thin aluminum strips. In the packaging field, it is essential for manufacturing foil and strip used in food containers, pharmaceutical wraps, and household packaging. The automotive industry benefits from its capability to create lightweight yet durable components such as body panels, radiators, and support structures. In construction, cold-rolled aluminum strips are commonly used for applications like roofing, curtain walls, window frames, and insulation systems. Furthermore, the electronics and electrical industries rely on these machines to produce materials for transformers, battery enclosures, cable shielding, and heat dissipation components.
Frequently Asked Questioins
Are you looking for machinery?Sky Bluer China is a leading manufacturer of wire rolling machines, specializing in the production of aluminum strip cold rolling mills, wire flattening and shaping equipment, and wire drawing machines. Our machines are engineered to ensure precise thickness reduction and outstanding surface finish quality.
Yes, annealing is usually necessary when producing aluminum strip using a rolling mill—especially during cold rolling.
So, while not required after every pass, annealing is a crucial step in producing high-quality, precision aluminum strip—especially in cold rolling applications. Let me know if you want to include furnace types or temperatures used!
It depends. In some cases, the equipment cannot be used universally due to varying cold rolling process requirements for different types of aluminum strips. Generally, annealing is performed after the strip reaches about 80% deformation, meaning the machines for composite aluminum strips and single-layer aluminum strips differ and are not interchangeable. While it is sometimes possible to produce both types on the same rolling mill, this requires specialized equipment and flexible machine configurations.
Worn or misaligned rolls can’t apply even pressure across the strip width, causing thickness variations and surface defects. To maintain product quality and protect equipment, it’s essential to realign the upper and lower rolls precisely using laser or mechanical alignment tools. If the roll has been ground multiple times, we recommend replacing it. We also provide the roll drawing for your reference.
Control system instability in aluminum cold rolling mills can arise from several factors. Slow, faulty, or uncalibrated sensors (like thickness or tension gauges) provide inaccurate feedback, leading to improper adjustments. Poorly tuned or outdated PLCs and control logic may fail to optimize the rolling process, causing delays in corrective actions. Additionally, signal lag between measurement and correction can occur due to slow processing speeds or inefficient communication systems. These issues result in inconsistent strip thickness, surface defects, and decreased product quality. Regular sensor calibration, system updates, and faster response times can help stabilize the control system and improve overall performance.
Related Production Lines
We Are Trusted Over 16+ Countries Worldwide
Are you in search of high-quality machinery for your production needs?
Sky Bluer China is a leading manufacturer of wire rolling machines, specializing in the production of aluminum strip cold rolling mills, wire flattening and shaping equipment, and wire drawing machines. Our machines are engineered to ensure precise thickness reduction and outstanding surface finish quality.