Introduction
In today’s competitive industrial landscape, speed, safety, and adaptability are critical. That’s where the steel flat wire production line makes a difference. Whether you’re producing stainless steel flat wire or carbon steel flat wire, Sky Bluer provides a reliable, modular solution trusted by wire manufacturers across Asia, the Middle East, and beyond.
This guide offers an in-depth look at flat wire rolling and drawing machine systems—exploring how they work, the advantages they offer over traditional setups, and why they’re considered the gold standard for demanding wire production environments.
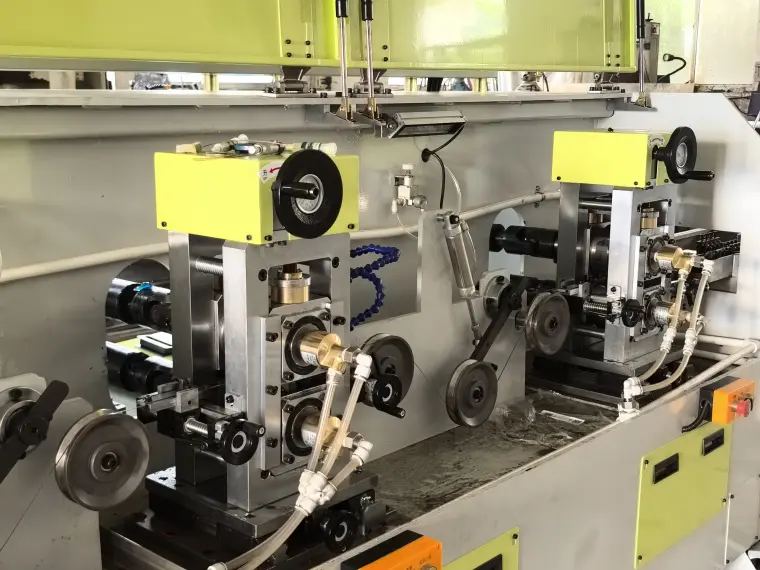
What is Production Process of Steel Flat Wire?
The production process of steel flat wire typically involves several key steps
- Wire Rod Preparation
High-quality steel wire rods are carefully selected and cleaned to remove surface impurities, as the quality of raw materials has a significant impact on the final product.
- Drawing Process
The wire rods are drawn through dies to reduce their diameter and improve mechanical properties. We provide comprehensive wire drawing machine solutions, featuring rod breakdown, intermediate, and fine wire drawing machines designed to handle a wide range of wire rod diameters with precision and efficiency.
- Annealing Process
The drawn wire is heat-treated to relieve internal stress and increase ductility. Annealing is a critical step in steel flat wire production that alleviates residual stresses induced by cold deformation during drawing and flattening processes. This heat treatment refines the microstructure, enhances ductility, and decreases hardness, thereby improving the wire’s formability and resistance to cracking or mechanical failure in subsequent processing stages. Proper annealing ensures that the final product achieves the required mechanical properties and dimensional stability, complying with stringent industry quality standards.
- Wire Flattening
The round wire is passed through precision rolling mills to achieve the desired flat shape and thickness. After this step, you will clearly see that the wire has transformed from its original round shape into a completely flat profile. We provide comprehensive wire drawing machine solutions, featuring 2 Hi rolling mill model and 4-hi rolling mill model.
- Straightening and Cutting
For fixed-length applications, the flat wire is straightened and cut. This step is also completed using specialized equipment. After the flat wire passes through the rolling mill, the next step is the straightening machine.
- Surface Treatment
Cleaning, coating, or polishing may be applied depending on final use.
- Quality Inspection and Packaging
Final products are inspected for dimensional accuracy and surface finish before being packaged for delivery.
Sky Bluer offers a complete flat wire production line covering each of these stages with high precision and reliability.
Steel flat wire flattening machines from Sky Bluer China, a leading manufacturer and supplier, are available in various sizes and capacities to meet diverse production needs. Designed for continuous, high-volume operation, these machines are ideal for large-scale industrial environments. Each metal flattener can be customized to handle specific wire diameters and deliver precise flat wire profiles. Widely trusted by global suppliers, Sky Bluer’s steel flat wire production lines offer high accuracy and efficiency in reshaping metal wire for specialized applications. With advanced control systems and flexible configurations, these flattening machines ensure consistent output, helping industries achieve superior product quality and meet strict dimensional requirements.
How Do Steel Flat Wire Mills Work?
The working principle behind a steel flat wire rolling mill is straightforward yet highly effective. These machines utilize the plastic deformation of metal to transform hot-rolled wire or strip steel into precise flat or strip-shaped wire profiles. The production process typically follows several key steps: rough drawing, annealing, flattening through precision rolling, take-up, and optional surface treatment. Through this sequence, the wire gradually achieves the desired shape, dimensions, and surface quality required for downstream applications.

Advantages of Steel Flat Wire Mills
Wire mills, such as wire flattening mills, Turks heads, and swagers, provide various advantages for industries that rely on ferrous and non-ferrous wire production. This section will cover a few significant benefits that these mills offer.
- Precise Shaping & Forming: Wire mills allow for the precise shaping and forming of wires, which is crucial for agriculture, medical devices, and military applications. Forming machines and payoffs/dereelers in wire mills ensure that the manufactured wires maintain uniform dimensions and meet exact specifications.
- Produce Specialized Products: The advanced technology employed by wire mills makes it possible to produce specialized products, such as wedge-shaped wires and superconducting materials. These cutting-edge wires are essential in innovative industries and allow manufacturers to stay competitive.
- Efficient & Cost-Effective: The streamlined production process minimizes waste and reduces labor costs. The efficient use of materials translates into less downtime and faster delivery of products to customers.
- Flexible Customization: Manufacturers can choose from various rebuilds, retrofits, and upgrades to meet their specific needs. This adaptability ensures that wire mills remain relevant and easily adjustable to meet evolving industrial requirements.
- Full automatic:Our equipment is fully automatic, providing seamless operation from pay-off (uncoiling) to take-up (coiling). The entire process is controlled by advanced automation systems, ensuring consistent quality, high efficiency, and minimal manual intervention throughout production.

Explore Wire Flattening Solutions From CRM
Steel Wire flattening mills play a critical role in flattening and shaping metal wire with precision, supporting industries like aerospace, electronics, and more. Using calibrated rollers and advanced controls, they ensure consistent, high-quality output.
With decades of experience, Sky Bluer leads in steel flat wire forming innovation. From standalone mills to fully automated lines, our custom solutions are built to maximize performance across materials and applications.
Whether you’re exploring new wire flattening&profiles or upgrading production, Sky Bluer is here to help. Contact us to see how our steel wire flattening and shaping technology can enhance your operations through innovation and precision engineering.
Frequently Asked Questions
What wire sizes and materials can the flattening machine handle?
CRM steel flat wire flattening machines are engineered to process a broad range of wire diameters—typically from 0.5 mm to 12 mm in raw material size—depending on the machine model and setup. They are capable of handling various metals, including stainless steel, carbon steel, copper, aluminum, brass, and specialty alloys. To meet diverse production needs, we offer fully customized configurations ideal for ultra-fine wires, high-tensile steel, and soft conductive materials commonly used in PV ribbon, busbar, and electronic applications.
Can the machine maintain tight thickness and width tolerances?
Yes. High-precision rolling mills are designed with advanced control systems to ensure tight dimensional tolerances, often within ±0.01 mm, depending on the material and application.
Is it possible to integrate the flattening line with existing production equipment?
Absolutely. Flattening machines can be customized for seamless integration with upstream drawing lines, annealing furnaces, and downstream take-up or surface treatment units.
What is the typical maintenance schedule for a wire flattening mill?
Our flat wire production line is designed as a standard, reliable system that requires minimal maintenance. Routine upkeep typically involves daily lubrication, roller inspections, and periodic calibration of the control systems. For optimal performance and longevity, a comprehensive preventive maintenance schedule is recommended every 6 to 12 months, depending on operational intensity.