Introduction
Our purpose for this blog is to showcase our company’s cutting-edge photovoltaic ribbon and tin coating production equipment, while providing insightful analysis of current and emerging market trends in the solar PV industry. Additionally, we aim to assist our users in anticipating future developments and strategic directions.
Technical Specifications of Photovoltaic Ribbon Tinning Line
This equipment is specifically engineered for the continuous production of Multi-Busbar (MBB) photovoltaic round welding ribbons.
- Solder wire diameter: 0.20–0.32 mm, with a dimensional tolerance of ±0.01 mm
- Elongation after tin coating: ≥ 25%
- Tensile strength of tinned ribbon: 65–75 MPa
- Surface quality requirements: The tinned ribbon must be free from visual defects such as deformation, pinholes, black spots, oxidation, or solder accumulations. Inspection is conducted via visual evaluation.
- Thickness tolerance: ±0.01 mm, measured with a precision digital micrometer
- Tin coating thickness: 15 μm ± 5 μm
- Concentricity deviation (metallographic inspection): ≤ ±0.08 mm
- Continuous production speed: ≥ 350 m/min
- Mechanical design speed: ≥ 400 m/min
MBB Ribbon Welding Equipment for TOPCon & BC Modules
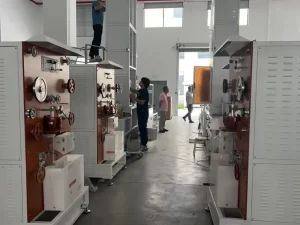
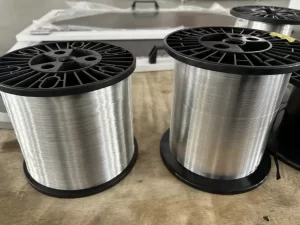
CRM-branded equipment is designed for the production of various MBB photovoltaic round welding ribbons used in TOPCon solar cells.
Our photovoltaic ribbon welding machines are widely applied in DBC (Double-sided Busbar Contact) modules, supporting module efficiencies of up to 24.8%.
BC (Back Contact) modules are equipped with a three-way junction box, a string-level arc fault rapid shutdown system, and a module-level intelligent rapid shutdown mechanism. The system can reduce the voltage to 0V within 1 second, effectively eliminating fire hazards during operation and addressing key safety concerns in photovoltaic power plants.
High-Efficiency PV Ribbon Tinning Machine Solution for TBC & THBC Modules
Our photovoltaic ribbon tinning machines are widely used in TBC and THBC modules, supporting mass production with module efficiencies up to 24.8% and power outputs exceeding 670W.
The THBC full back-contact design eliminates front-side grid shading and removes the need for main busbars on the rear, resulting in an excellent temperature coefficient and outstanding energy yield performance. This advanced architecture enables module efficiencies of up to 25.5%.
Development Trends in the Solar Photovoltaic Ribbon Industry
BC Technology Gains Momentum in the Post-TOPCon Era
Following a year of intense competition between TOPCon and BC technologies, the latest wave of mainstream photovoltaic equipment has revealed a clear trend: many leading Chinese manufacturers have chosen to showcase their BC (Back Contact) modules in what is considered the “final exam” of PV technology selection.
Currently, BC modules have become the most widely promoted and adopted solution in the market. It is estimated that around 30% of solar cell and module manufacturers have already launched BC-based products, while adoption among top-tier enterprises has reached as high as 80%, signaling a strong industry shift toward back-contact solutions.
BC Modules Dominate at This Year’s SNEC2025 Exhibition
After a year of ongoing competition between TOPCon and BC technologies, this year’s SNEC exhibition became the “final exam” for photovoltaic innovation—with many companies opting to showcase their BC (Back Contact) modules. Notably, over 80% of leading manufacturers presented BC module solutions, highlighting a significant shift in industry focus and market momentum.
Conclusion
Sky Bluer China actively drives the future of PV ribbon technology by delivering high-performance, precision-engineered equipment tailored for emerging solar cell types such as TOPCon, BC, TBC, and THBC. We respond to market demands for greater efficiency, reliability, and sustainability through continuous innovation in materials, automation, and intelligent manufacturing. As global trends shift toward advanced interconnection solutions and safety-focused module designs—clearly reflected at SNEC 2025—Sky Bluer China remains committed to supporting the photovoltaic industry’s transition with cutting-edge, Made-in-China solutions that empower manufacturers to stay ahead in a competitive landscape
Sky Bluer China not only aligns with the latest industry trends but actively drives them by delivering state-of-the-art PV ribbon production and tinning equipment. Our solutions are engineered to meet the evolving demands of high-efficiency solar technologies—such as MBB, TOPCon, and BC modules—while advancing automation, sustainability, and precision manufacturing across the photovoltaic value chain
Playlist
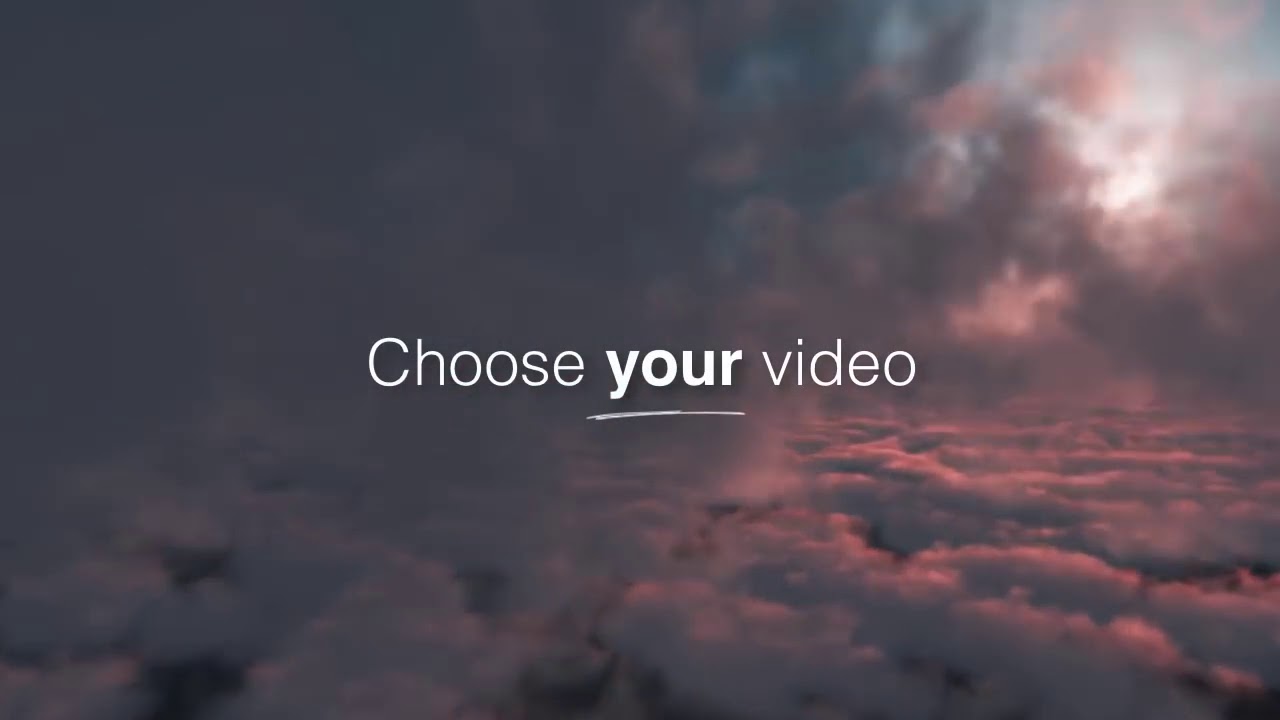
0:16
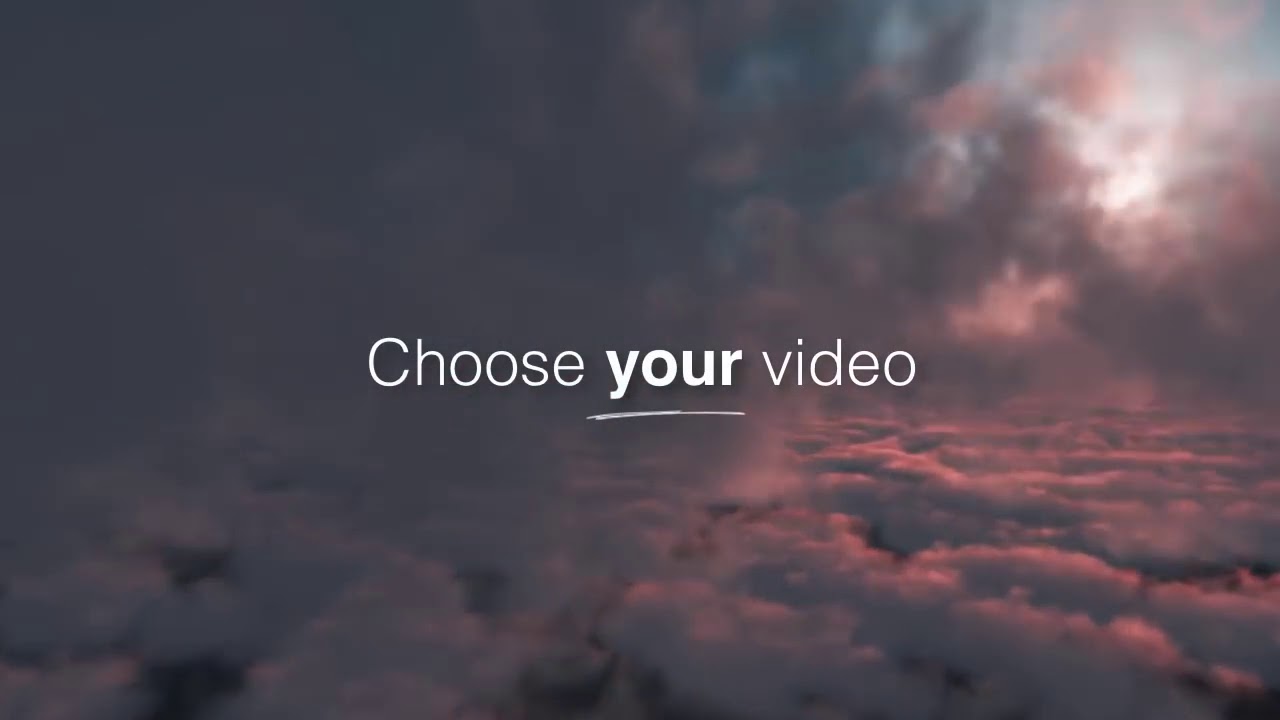
0:16
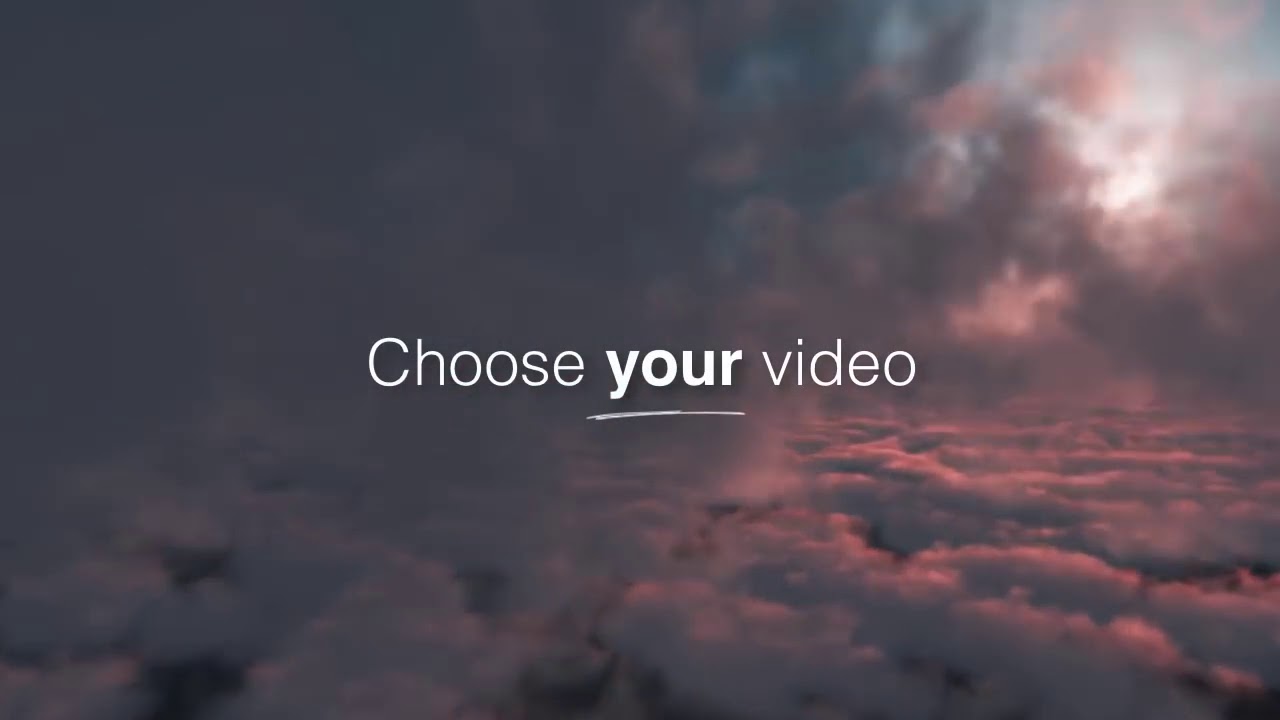