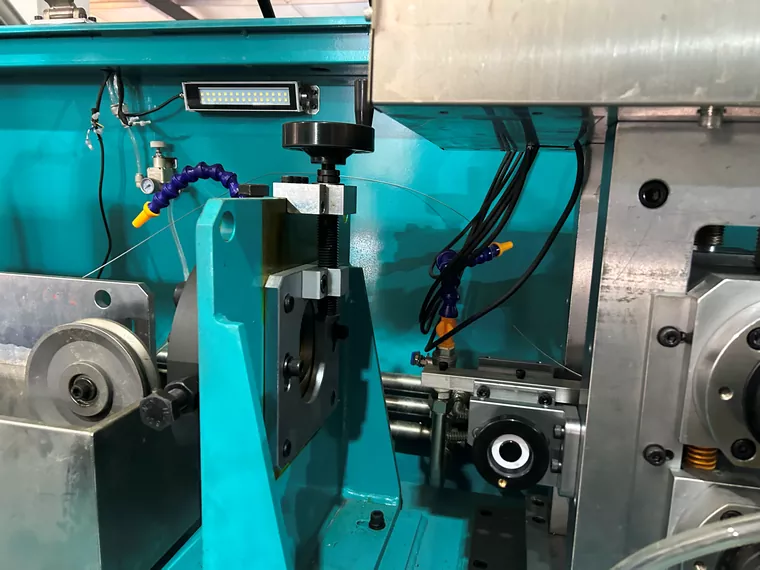
Stainless Steel Flat-Wire Equipment
Sky Bluer China Company manufactures stainless steel flat-wire equipment designed to produce high-precision flat wire with fully rounded edges from round wire and bars. The production line primarily consists of a payoff machine, rolling mills, dancers, straightening machines, and precision wire take-ups.
Details of Stainless Steel Flat-Wire Equipment
Stainless steel flat-wire equipment is a dedicated system engineered to transform round wire or bars into precisely shaped flat wire with accurate dimensions, refined surfaces, and tailored mechanical properties. This machinery plays a crucial role in manufacturing flat wire for various industries, including medical technology, electronics, aerospace, and automotive sectors, where precision and quality are paramount.
- Main Grades of Stainless Steel Flat Wire:
- Advantages of Cold-Rolled Stainless Steel Flat-Wire Equipment
- Stainless Steel AISI 302 alloy, AISI 304 alloy, 304 Stainless Steel 1/4 Hard per ASTM A240, A480 and A666, AISI 316 alloy, AISI 316L alloy, AISI 321 alloy, 17-7PH alloy, AISI 410 alloy, AISI 420 alloy,
Main Technical Specifications for Stainless steel flat-wire equipment - Input size: Round wire/bar Up to 12mm
- Typical Output size: 0.120” thick+/-.003 x .600” wide+/- .005
Shapes: flat wire with fully rounded edges - Working Speed: 20–450m/min
- Packing: oscillate wound
ID:12-20", OD: 26-28''
Face: 6-8''
Sky Bluer's cold-rolled stainless steel flat-wire equipment offers superior performance compared to drawn flat wire of the same width-to-thickness ratio. It provides a larger cast, reduced camber, and minimized internal stress.
Key benefits include:
• Improved straightness through stress relieving, making it ideal for applications requiring high precision.
• Options for tighter spool packaging for enhanced efficiency.
• Availability of optional textured surfaces to meet specific application needs.
• The standard width tolerance is ±10% of the nominal width, rounded up to the nearest 0.0025 mm (0.0001 in), with a minimum tolerance of ±0.0076 mm (±0.0003 in).
• Our machine features a simple and user-friendly design, allowing for quick roll changes in just three minutes while ensuring effortless operation.
• We ensure a short delivery time, with conventional model delivered within 30 days and non-standard models within 50-60 days.
Common Applications of Flat Wire
- Sky Bluer China supplies high-precision flat wire for a wide range of medical and industrial applications, including:
Percutaneous catheters - Neurovascular and endovascular devices
- Self-expanding stents and delivery systems
- Coronary stents
- Stone retrieval baskets
- Catheter-based heart pumps
- Orthodontic clips
- Suture passers
- Oil well screensOur flat wire plays a crucial role in advancing medical technology, ensuring reliability and performance in critical applications.
Frequently Asked Questioins
The number of rolling stages depends on the required total reduction in thickness, the reduction per stage, and the specific properties of the wire. A good balance between the number of stages and material quality must be achieved for optimal results.
The rolling mill, also known as a flattening mill or 2Hi rolling mill, is a critical step in the rolling process. It transforms round wire into flat wire, ensuring a successful and precise conversion. Sky Bluer China uses the rolling mill to transform round wire or bars into high-precision flat wire, controlling its thickness, width, and surface finish. The mill reduces the wire's thickness, adjusts its width, and ensures smooth, rounded edges for top-quality results. Through cold rolling, the process enhances the wire's mechanical properties, such as tensile strength and stress resistance, by refining the grain structure. Sky Bluer China ensures consistency in dimensions and surface quality throughout the wire length, making it perfect for demanding applications like stents, catheters, and orthodontic components. The rolling mill delivers a durable, uniform, high-precision flat wire.
This is a common question among customers, as the machines used to produce these two types of wire differ, and their applications span across distinct industries.
The key difference between flat wire with rounded edges and flat wire with sharp edges lies in their edge profiles and applications.
Flat wire with rounded edges has smooth, curved edges, making it ideal for medical devices like stents, catheters, and orthodontic clips. The rounded edges reduce the risk of damage to surrounding tissues and prevent wear in high-precision applications.
Flat wire with sharp edges, on the other hand, has angular, defined edges, which are suitable for industrial applications where precision cutting or other functions requiring sharpness are needed.
In essence, rounded-edge flat wire is preferred for safety and smoothness in sensitive applications, while sharp-edge flat wire is used in industries that demand more defined and precise edge geometry
Yes, annealing is often a crucial step in manufacturing stainless steel flat wire with rounded edges, especially when the wire needs to be softened to enhance flexibility and ease of processing. Annealing is a heat treatment that relieves the stresses introduced during cold working, ensuring that the wire possesses the desired properties like strength and ductility.
Typically, after processes like drawing or rolling, annealing is required to achieve the proper mechanical characteristics for applications in industries such as construction or manufacturing. However, if the raw materials are already annealed, the wire will be softer and more malleable, eliminating the need for additional annealing. Our factory offers a variety of annealing furnaces to suit your specific industry needs and production requirements. With our comprehensive solutions, you can rest assured that we provide everything you need, delivering a seamless one-stop supply experience.
To determine the number of rolling stages required based on the width-to-thickness ratio of the finished flat wire, consider the following process:
1. Calculate the Desired Width-to-Thickness Ratio:
First, Calculate or determine the desired width-to-thickness ratio of the finished flat wire. This ratio is a key specification for the end product, influencing factors such as flatness, appearance, tensile strength, yield strength, and overall mechanical properties.
2. Establish the Initial Wire Dimensions:
Determine the initial diameter (or thickness) of the round wire or bar before cold rolling. The starting thickness will influence how much reduction is needed at each stage.
3. Define Reduction per Stage:
The reduction per rolling stage depends on the rolling mill and material. For most spring flat wire processes, the reduction per stage is generally between 10% and 40% of the wire's thickness. However, this varies depending on the material properties and equipment.
4. Determine the Total Reduction Needed:
To reach the desired width-to-thickness ratio, calculate the total reduction in the wire's thickness by comparing the starting thickness and the desired final thickness. But there are many cases where this is not realistic.
5. Estimate the Number of Rolling Stages:
Divide the total required reduction by the average reduction per stage. For example, if you need to reduce the stainless and steel wire's thickness by 80% and the average reduction per stage is 20%, you will need approximately 4 rolling stages (80% ÷ 20%).
6. Consider Material and Process Limits:
Keep in mind that rolling limits, stainless steel raw material type, and quality requirements (such as surface finish and mechanical properties) might influence the number of stages. For example, materials that are harder or have more complex properties may require additional stages or specific heat treatments between stages.
7. Judge by experience
For example, we have years of experience in the production and manufacturing of rolling mills and wire drawing machines. We often rely on this expertise to determine the number of rolling mills required. Take producing stainless steel flat wire with dimensions of 1.23x6.52, for instance. According to calculations, three rolling mills would be needed. However, in our daily production, we have found that two rolling mills are more than sufficient to meet the requirements. Therefore, we make judgments based on our practical experience.
Related Production Lines
We Are Trusted Over 16+ Countries Worldwide
Founded in 2016, Sky Bluer Industries is a leading manufacturer of wire rolling mills, specializing in fine wire, flat wire, square wire, wedge wire, and shaped wires equipment. Our mission is to design state-of-the-art drawing machines tailored to meet the unique production needs of each customer.
With 80% of our machines exported to European countries, we are committed to providing fast, durable, and user-friendly wire machinery to customers worldwide. Our product range includes straight-line wire drawing machines, wet wire drawing machines, inverted vertical drawing machines, and ultra-fine wire drawing machines—all engineered for precision and efficiency.
No matter the industry or application, Sky Bluer Industries is your trusted partner for high-performance wire processing solutions.